В объективе – ОАО «Речицадрев». Новый рекорд завода ДСП
Источник: Dneprovec.by Фото: автора

За последнее время на заводе ДСП провели ряд модернизаций оборудования, стали использовать новые виды смол производства ОАО «Речицадрев». Работникам пришлось заново учиться, повышать свою квалификацию. Всё это привело к повышению скорости производства – с 330 до 420 метров в секунду – и, как следствие, к новому рекорду: 24 650 кубических метров древесно-стружечной плиты за июль, притом что проектная мощность завода составляет 17 500! Мы поговорили с заводчанами о причинах и предпосылках такого качественного рывка, новом ритме работы и, конечно, о роли человеческого фактора.
Алексей Марченко, начальник производства:

– Идея выйти на новые скорости назрела давно. Спрос на нашу продукцию растет, и мы должны были быть готовы его удовлетворить. Около трех месяцев назад в тестовом режиме пытались выйти на высокие показатели, но некоторые производственные участки нам не позволяли этого сделать. Выявив «слабые звенья», мы приступили к модернизации. Весь коллектив завода ДСП принимал участие в этом процессе, анализировали, генерировали идеи для улучшения работы оборудования. Нам здорово помогли работники ремонтно-механического цеха, которые изготовили из металла необходимые заготовки.
Конечно, без наших коллег с завода синтетических смол выход на новые скорости был бы невозможен. Именно они сумели подобрать такую рецептуру, которая сохраняет все физико-механические показатели смолы при повышенных скоростях производства. Мы действовали в тесной спайке, путем экспериментов приспосабливая состав смолы и режим производства древесно-стружечных плит друг к другу.
* * *
Процесс изготовления ДСП начинается с этапа подготовки материала в сушильном отделении. И здесь мы модернизировали процесс разгрузки бункера сырой стружки. Бункера сухой стружки внутреннего и наружного слоев также подверглись усовершенствованию, что позволило обеспечивать подачу нужного объема сырья для поддержания высокой производственной скорости.
В главном корпусе мы провели модернизацию системы охлаждения смесительных агрегатов, что позволило работать с повышенными температурами, которые возникают при высоких скоростях подачи материала. Стружка горячая, около 80-90 °С, следовательно, нагреваются смесительные агрегаты. И для того чтобы смола раньше времени не отверждалась, необходима наладка охлаждения – это и было сделано. Даже в жаркий июль мы смогли обеспечить нужную температуру.
Нам удалось провести модернизацию оборудования совместно с проведением плановых профилактических работ, то есть производство дополнительно не останавливалось, его объемы не падали.
Каждому из нас пришлось заново входить в рабочий режим, менять настройки, проводить очень тщательный анализ оборудования, применять весь свой опыт и профессионализм. За это им – отдельная благодарность. Конечно, увеличение объемов производства самым непосредственным образом сказалось на их заработной плате. А еще мы решили установить в пультовую новые удобные кресла и кофе-машину. Мелочь, а приятно. Такое небольшое зримое подтверждение того, что труд рабочего человека у нас ценится!
Евгений Руденко, оператор сушильного оборудования:

– Я работаю здесь с самого открытия нового завода ДСП, уже лет восемь! Режим такой: четыре через четыре – две дневные, две ночные смены. График напряженный, но мы к нему привыкли. Суть работы: на оборудование поступает сырая стружка, которая должна быть высушена при определенной температуре, влажности. Нужно контролировать режимы работы сушильного оборудования, редлеров, анализировать все параметры.
При новых скоростях повышается температура, поступает больше сырья. Ответственность больше – приходится уделять внимание и стружечному отделению, чтобы поступал необходимый объем. Если я не услежу на своем участке за технологией, будет нарушен весь производственный процесс. Не выберешь правильный режим работы оборудования, подведешь своих коллег, весь завод. Но осваивать что-то новое для меня не в диковинку, я раньше работал на формашине, также повышал квалификацию во время модернизации завода. Точно так же, как и все мои коллеги: у нас есть мотивация, есть стремление развиваться, трудиться ради собственного благополучия и на благо всего предприятия.
Иван Кулеш, оператор формирующей машины:
– Моя задача – контролировать процесс формирования ковра. К нам поступает осмоленная, подготовленная стружка. Плита ДСП состоит из трех слоев, а формашина эти слои укладывает.

Мы не могли работать на больших скоростях из-за недостатка сырья. После модернизации системы разгрузки бункеров этот нюанс был исправлен, и мы заработали на полную мощность. Изменился в целом весь режим: поменялась рецептура, дозировка смоления, формировка ковра, насыпка.
Такие изменения внедрялись постепенно, последовательно, было время освоиться, привыкнуть к скоростям. Главное – внимание, анализ и контроль! Ответственность и нагрузка на операторов растет, но растет и некий хороший рабочий азарт, понимание собственной значимости. Когда нравится своя работа, когда вокруг люди, которые горят делом, то всё спорится. Я вижу: у коллег как будто открылось второе дыхание, такой ритм бодрит. У нас отличные отношения в коллективе, все ребята молодые, лет тридцати–сорока, так что общий язык находим, сотрудничаем, доверяем друг другу: от начальника производства до оператора за пультом!
Андрей Скопич-Шмидт, прессовщик древесных и кастровых плит:
– Я работаю на одном из завершающих этапов производственного цикла. Сейчас трудимся практически на максимуме, загружено оборудование, выкладываются на полную люди. Приходится себя подстегивать, поднимать свой профессиональный уровень.
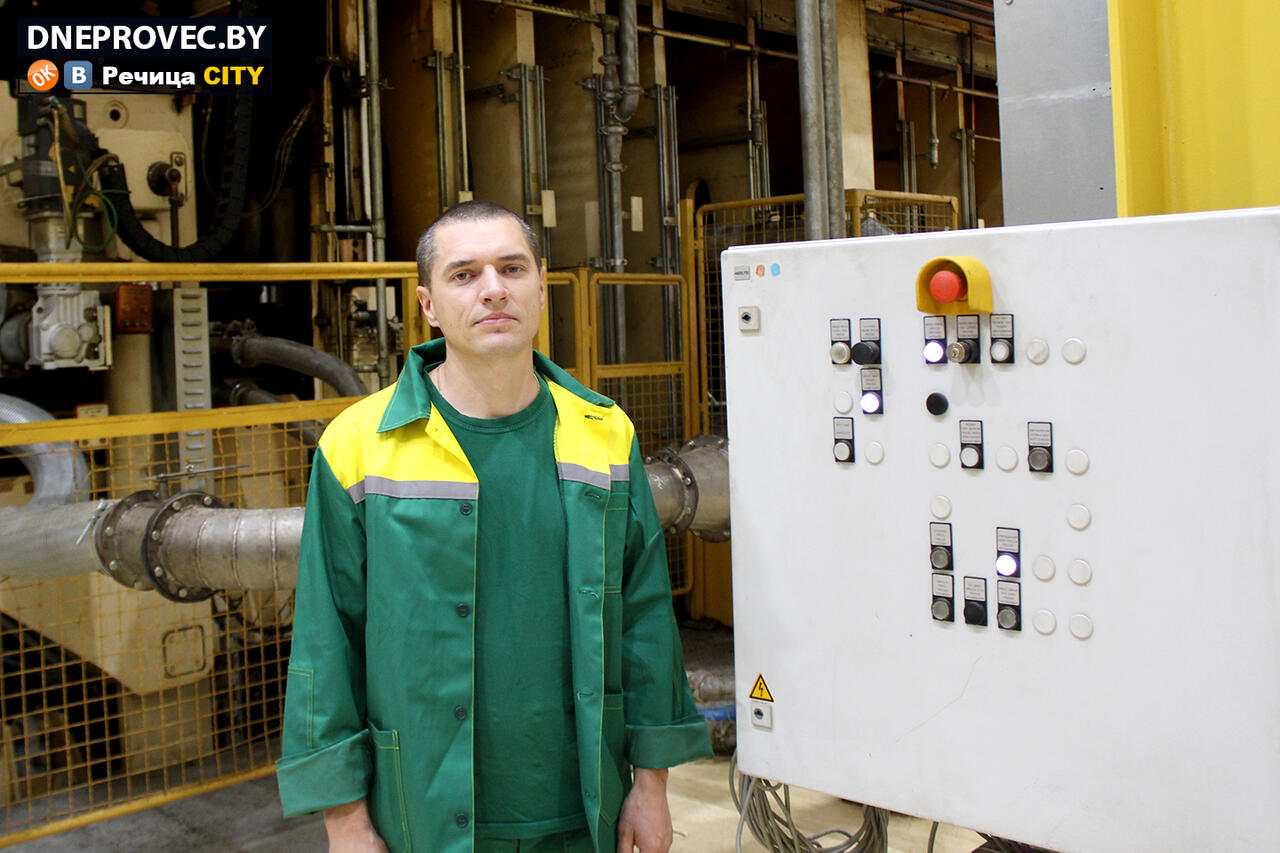
Представьте себе: огромные пресс, почти 25 метров, гидравлические цилиндры, которые создают давление в определенных зонах. Этот процесс нужно контролировать, чтобы лента не убежала, чтобы качество продукции было эталонным. Ответственность большая! Хочу отметить, что у нас на производстве, конечно, спрос серьезный, но видна и настоящая забота о людях. Мне есть с чем сравнить, я работаю на «Речицадреве» 17 лет, видел еще старый завод. Это небо и земля – то, что было, и то, что мы имеем сейчас. Спортзал, душ, буфет, комната приема пищи, дополнительные 70 рублей на питание, холодильники, микроволновки, уютные раздевалки, кондиционер в пультовой. А еще очевидная зависимость размеров заработной платы от качества и количества выполненной работы. И, главное, – тот самый командный дух, когда после трудовой смены ИТР и простые рабочие вместе играют в футбол, общаются на равных. Без этого ни о каких рекордах и речи бы не было!
Дмитрий Стрельченко, ведущий механик:
– Модернизация не происходит по щелчку. Сначала появляются какие-то задумки, которые обсуждаются коллегиально. Действует коллективный разум, в одиночку тут ничего не добьёшься.

Повторюсь, работа совместная, завязаны были все – от начальника производства до сварщика. Начальник технической службы, ведущий механик, ведущий энергетик, слесарь, электрик – не важных людей в этом процессе не было.
Многие комплектующие изготавливались у нас, на заводе. Например, детали, позволяющие захватывать больший объем стружки. Усовершенствование бункеров, редлеров, приводов – всё это вкупе дало увеличение объема подаваемой стружки, что позволило нарастить скорость и кубатуру.
Мы не закупали комплектующие на стороне, наших технологий, квалификации, смекалки хватило для того, чтобы их изготовить. В ремонтно-механическом цехе есть и плазменная резка, и другие металлообрабатывающие станки. Работники наши – профессионалы своего дела, так что каких-то сторонних фирм, специалистов привлекать не пришлось.
Конечно, мы бываем на других предприятиях, перенимаем опыт, но специфика везде своя, и бездумное копирование в нашей отрасли попросту невозможно. Так что наши достижения и рекорды – результат труда работников «Речицадрева» на оборудовании, модернизированном собственными силами, и этим стоит гордиться!
Факты:
Современное автоматизированное производство было построено на месте прежнего. Монтаж начался 11 февраля 2013 года. В мае 2014 года
завод официально был введен в эксплуатацию. Кроме того, на предприятии действует линия по выпуску ламинированной плиты (годовой выход продукции 8 000 000 м2). В мае 2015 года была введена в эксплуатацию линия по импрегнированию декоративной бумаги.
Расширение производственных площадей, приобретение и установка нового технологического оборудования с программным управлением, энергосберегающими характеристиками позволили поднять на современный уровень многие производственные процессы, выпускать качественную продукцию, отвечающую всем запросам потребителей, как в нашей стране, так и за рубежом.
Перепечатка текста и фото Dneprovec.by запрещена без разрешения редакции. info@dneprovec.by